sheet metal trimming process Sheet metal cutting, a fundamental process in the metalworking industry, involves the precise removal of material from sheet metal stock to form a specific part or component. This process, essential in shaping the metal sheet . These 2 box detectors that would find deep caches. Watching hundreds of detecting videos, you don't see them used at all. There are a few YouTube videos and they all look like OLD surplus people have picked up.
0 · sheet metal operations with diagrams
1 · sheet metal manufacturing process types
2 · sheet metal manufacturing process pdf
3 · perforating operation in sheet metal
4 · notching operation in sheet metal
5 · how to fabricate sheet metal
6 · cutting clearance for sheet metal
7 · blanking operation in sheet metal
Twist lock receptacle for mounting in junction box. 20A 230V.
In the realm of sheet metal manufacturing, trimming is a shearing process that removes excess material from a formed part. It is a crucial step that helps to achieve the desired size, shape, and finish, ensuring the .
Trimming is the process of cutting away any unwanted or excess material from the sheet metal part. This process not only results in a smoother edge finish, enhancing the part’s appeal and safety, but it also ensures that .
sheet metal operations with diagrams
sheet metal manufacturing process types
Slotting is a sheet metal process where a slot is put in the metal to do its job. Also known as slitting, the machines used in the process are called slitting machines. The process involves cutting notches in the steel sheets and .Trimming is the removal of excess metal from a stamped part to allow the part to reach the finished stage or to prepare it for subsequent operations. This article presents an analysis of . Sheet metal cutting, a fundamental process in the metalworking industry, involves the precise removal of material from sheet metal stock to form a specific part or component. This process, essential in shaping the metal sheet .Trimming. Deburring. 1. Shearing Process. Sheet Metal Shearing Operation. Shearing is a type of sheet metal cutting process. It involves cutting a sheet in a straight line or at an angle. It is preliminary used to cut a larger sheet into .
Sheet metal manufacturing is the process of creating sheet metal parts by cutting, bending, and forming thin metal sheets into specific shapes and sizes. The process typically uses coating, cutting, bending, and assembly techniques.Cutting processes are those in which a piece of sheet metal is separated by applying a great enough force to caused the material to fail. The most common cutting processes are performed by applying a shearing force, and are . This sheet metal forming process is often used for vehicle body parts, enclosures, and electrical components. It can be performed on most compatible sheet metal forming materials, like stainless steel, brass, .Sheet metal trimming is a basic process used for thousands of products; however, not all factories start with an optimized trimming process, which may hinder the development time and cost of a new stamping project. We discuss how .
Shearing is a type of sheet metal cutting process. It involves cutting a sheet in a straight line or at an angle. It is preliminary used to cut a larger sheet into small sheets for further processing. Sheet metal shearing machine. Shearing .Slitting is a sheet metal cutting process with circular knives, which is used to split wide coiled sheet metal into narrower widths or for edge trimming of rolled sheet. The slitting process is schematically shown in Figure 1.6. The slitter knives are mounted on two arbors together with spacers . The spacers determine the width of the cut and . The sheet metal trimming process, an integral part of the sheet metal manufacturing cycle, requires a comprehensive understanding to troubleshoot common defects. Trimming in the context of sheet metal manufacturing is a final operation where excess material is cut away to bring the metal part closer to its intended shape or size.
Sheet metal routing Creator of the “bridge-cut” process, CRENO aluminum stack routers automate the sheet trimming process with a very high level of productivity and quality. This solution offers: Complete supervision of the process for each machining sequence Multiple aluminum sheets up to 12mm (0.47 inch) Single steel sheets up to 2.5mm (0.01 inch) Three [.] Sheet metal cutting is a fundamental process in manufacturing that involves various techniques such as laser, plasma, and waterjet cutting. This article provides a comprehensive guide to these methods, exploring the principles behind each and their applications. From understanding the equipment used to the intricacies of different cutting . Hi Friends,In this video you will learn Different types of Cutting operation in sheet metal | Sheet metal cutting operationsShearingCutoff Parting offBlankin.
The shaping and forming of metal sheet is a key manufacturing process. Incremental Sheet Forming (ISF) is a novel sheet metal forming technology where the deformation of the metal sheet occurs . Pinch trimming is a rather unconventional metal cutting process, because it does not employ some of the basic guidelines associated with conventional cutting. Think of pinch trimming as a metal squeezing process in which the metal is pinched on a vertical wall to the point at which it is separated from the scrap. Unlike conventional cutting . Slitting is an important part of the overall sheet metal cutting process since it is needed to create sheet metal pieces of a specific width for other machines to be able to cut them properly. Since sheet metal mostly arrives in the form of the coil to the factory, it is fairly common for slitting to be used as the first part of the sheet metal .After meticulous material selection, the next stage in sheet metal fabrication is cutting the metal into the desired shape and size as per the design specifications. This step is vital for setting the foundation of the final product. Here are three key steps in the metal cutting process:
sheet metal manufacturing process pdf
During the stamping process and cutting phase, the metal sheet is placed in a press, where a punch forces it through a die. This action shears the metal deformation along the die’s edges to produce the desired part. The blanking process typically yields clean, smooth edges, although there may be instances of rough edges or burrs that need . The sheet metal cutting process is an important part of fabrication or metalworking, beginning with choosing the appropriate material and defining the desired shape and size. To remove superfluous material from a metal sheet, many cutting procedures are used, including shearing, laser cutting, water jet cutting, and plasma cutting. .Sheet metal manufacturing is the process of creating sheet metal parts by cutting, bending, and forming thin metal sheets into specific shapes and sizes. The process typically uses coating, cutting, bending, and assembly techniques. . Shaving/Trimming is a finishing operation in which shearing off of burrs from the cut edges is carried out in order to make the edges smooth and also impart .
The sheet metal cutting process is a particularly important part of fabricating sheets of metal into components of a wide array of consumer and industrial products. Used to remove unneeded material, shearing involves the . It works exceptionally well for sheet metal and thin materials. Water Jet Cutting: Advantages and Applications. Water jets mix water with abrasive particles to cut metal. This cold-cutting process prevents heat distortion. It cuts thick materials while maintaining material properties. Plasma Cutting: A Popular Method for Metal Fabrication .
5. Sheet Metal Cutting. Sheet metal cutting is done to remove the metal in a particular shape out of the larger sheet of metal. The two categories of sheet metal cutting are bevel and spur gear cutting. The former refers to the process of cutting sheets at an angle, usually at 30 degrees. Meanwhile, the latter is cutting metal sheets in the .
Components aiding in the sheet metal notching process are assembled, which comprise of work surface, the punch press and measuring tools. . In tube notching, different angle cutting are made on the metal tube. Speed: A sheet metal notching is fast hence an advantage to the cycle time.Blanking is a cutting process in which a piece of sheet metal is removed from a larger piece of stock by applying a great enough shearing force.In this process, the piece removed, called the blank, is not scrap but rather the desired part.Blanking can be used to cutout parts in almost any 2D shape, but is most commonly used to cut workpieces with simple geometries that will be . Sheet metal cutting, a fundamental process in the metalworking industry, involves the precise removal of material from sheet metal stock to form a specific part or component. This process, essential in shaping the metal sheet into a finished part, employs various tools and techniques, ensuring accuracy and efficiency. Sheet metal blanking process. Blank sheet metal fabrication is a versatile and efficient manufacturing process that involves cutting flat sheet metal into predefined shapes or profiles. It is also known as shearing, a process used to remove a part from a sheet of metal by applying a force strong enough to separate the material cleanly.

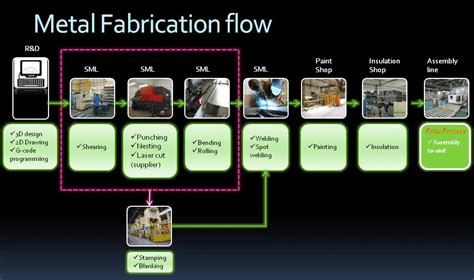
Factors Affecting Metal Cutting. Some of the factors that affect metal cutting are: Cutting speed: The relative speed between the cutting tool and the workpiece. Feed: The rate at which the cutting tool advances into or along the workpiece. Depth of cut: The thickness of the layer of material removed by one pass of the cutting tool. Cutting tool material: This is a . The key types of cutting operations are shearing, blanking, punching, and trimming. Engineering analysis of sheet metal cutting considers process parameters like clearance between the punch and die, stock thickness, material properties, and cut length. The cutting force is estimated based on the material shear strength, thickness, and cut length.The sheet metal stamping process is a strategic advantage that can set your business apart. Precision, efficiency, and innovation are at its core, driving the production of high-quality components. Precision, efficiency, and innovation are at its core, driving the production of high-quality components.
In general, each piece of sheet metal is put between two different parts of the cutting process. The upper part is known as a punch, while the lower part is known as a die. Technically, each of these components can be referred to as a die, but to distinguish one from the other, the upper part is given a separate name.
perforating operation in sheet metal

notching operation in sheet metal
how to fabricate sheet metal
cutting clearance for sheet metal
Build test fixtures, prototypes, and other small structures with this miniature version of T-slotted framing and fittings. Build lightweight structures, such as light duty machine guards, enclosures, and carts, with framing that is two-thirds the weight of aluminum framing.The room is limited so I don't want a stand and would rather put a metal pole into the ground in a corner, about a foot from two fences. Just wondering how deep thd pole needs to be, what .
sheet metal trimming process|sheet metal manufacturing process types